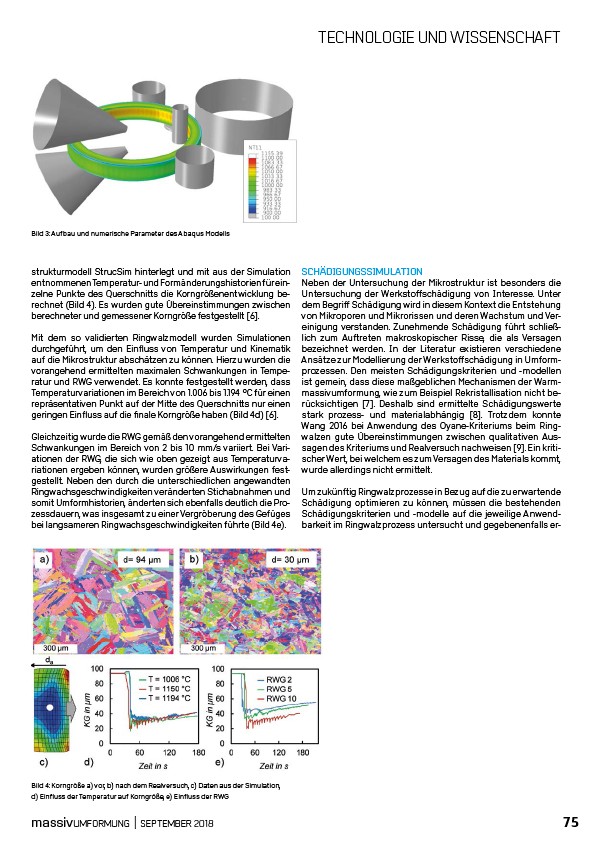
Bild 3: Aufbau und numerische Parameter des Abaqus Modells
strukturmodell
StrucSim hinterlegt
und mit aus der Simulation
entnommenen
Temperatur
und Formänderungshistorien
für einzelne
Punkte des Querschnitts
die Korngrößenentwicklung
berechnet
(Bild 4). Es wurden
gute Übereinstimmungen
zwischen
berechneter
und gemessener
Korngröße
festgestellt
6.
Mit dem so validierten
Ringwalzmodell
wurden Simulationen
durchgeführt,
um den Einfluss
von Temperatur
und Kinematik
auf die Mikrostruktur
abschätzen zu können. Hierzu
wurden die
vorangehend
ermittelten
maximalen
Schwankungen in Temperatur
und RWG verwendet.
Es konnte festgestellt
werden, dass
Temperaturvariationen
im Bereich
von 1.006 bis 1.194 °C für einen
repräsentativen
Punkt auf der Mitte des Querschnitts
nur einen
geringen Einfluss
auf die finale Korngröße
haben (Bild 4d) 6.
Gleichzeitig
wurde die RWG gemäß
den vorangehend
ermittelten
Schwankungen
im Bereich
von 2 bis 10 mm/s variiert. Bei Variationen
der RWG, die sich wie oben gezeigt
aus Temperaturvariationen
ergeben
können, wurden größere Auswirkungen
festgestellt.
Neben den durch die unterschiedlichen
angewandten
Ringwachsgeschwindigkeiten
veränderten
Stichabnahmen
und
somit Umformhistorien,
änderten
sich ebenfalls
deutlich
die Prozessdauern,
was insgesamt
zu einer Vergröberung
des Gefüges
bei langsameren
Ringwachsgeschwindigkeiten
führte (Bild 4e).
UND WISSENSCHAFT
SCHÄDIGUNGSSIMULATION
Neben der Untersuchung
der Mikrostruktur
ist besonders
die
Untersuchung
der Werkstoffschädigung
von Interesse.
Unter
dem Begriff
Schädigung
wird in diesem
Kontext
die Entstehung
von Mikroporen
und Mikrorissen
und deren Wachstum
und Vereinigung
verstanden.
Zunehmende
Schädigung
führt schließlich
zum Auftreten
makroskopischer
Risse, die als Versagen
bezeichnet
werden.
In der Literatur
existieren
verschiedene
Ansätze
zur Modellierung
der Werkstoffschädigung
in Umformprozessen.
Den meisten Schädigungskriterien
und -modellen
ist gemein, dass diese maßgeblichen
Mechanismen
der Warmmassivumformung,
wie zum Beispiel Rekristallisation
nicht berücksichtigen
7. Deshalb
sind ermittelte
Schädigungswerte
stark prozess
und materialabhängig
8. Trotzdem
konnte
Wang 2016 bei Anwendung
des Oyane-Kriteriums
beim Ringwalzen
gute Übereinstimmungen
zwischen qualitativen
Aussagen
des Kriteriums
und Realversuch
nachweisen
9. Ein kritischer
Wert, bei welchem es zum Versagen
des Materials
kommt,
wurde allerdings
nicht ermittelt.
Um zukünftig
Ringwalzprozesse
in Bezug auf die zu erwartende
Schädigung
optimieren
zu können,
müssen die bestehenden
Schädigungskriterien
und -modelle
auf die jeweilige
Anwendbarkeit
im Ringwalzprozess
untersucht
und gegebenenfalls
erTECHNOLOGIE
Bild 4: Korngröße a) vor, b) nach dem Realversuch, c) Daten aus der Simulation,
d) Einfluss der Temperatur auf Korngröße, e) Einfluss der RWG
massivUMFORMUNG | SEPTEMBER 2018 75