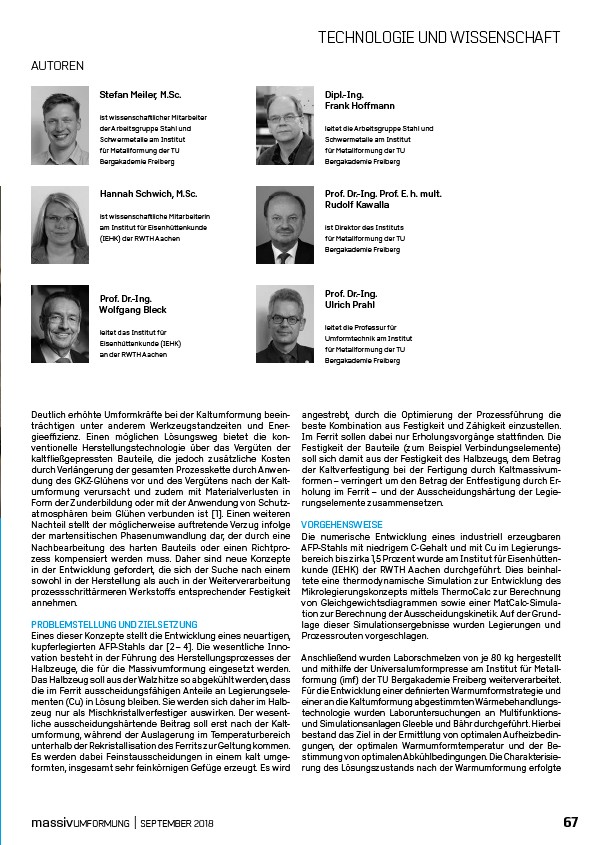
TECHNOLOGIE UND WISSENSCHAFT
AUTOREN
Stefan Meiler, M.Sc.
ist wissenschaftlicher Mitarbeiter
der Arbeitsgruppe Stahl und
Schwermetalle am Institut
für Metallformung der TU
Bergakademie Freiberg
Hannah Schwich, M.Sc.
ist wissenschaftliche Mitarbeiterin
am Institut für Eisenhüttenkunde
(IEHK) der RWTH Aachen
Prof. Dr.-Ing.
Wolfgang Bleck
leitet das Institut für
Eisenhüttenkunde (IEHK)
an der RWTH Aachen
Deutlich
erhöhte Umformkräfte
bei der Kaltumformung
beeinträchtigen
unter anderem Werkzeugstandzeiten
und Energieeffizienz.
Einen möglichen
Lösungsweg
bietet die konventionelle
Herstellungstechnologie
über das Vergüten
der
kaltfließgepressten
Bauteile,
die jedoch zusätzliche
Kosten
durch Verlängerung
der gesamten
Prozesskette
durch Anwendung
des GKZ-Glühens vor und des Vergütens
nach der Kaltumformung
verursacht
und zudem mit Materialverlusten
in
Form der Zunderbildung
oder mit der Anwendung
von Schutzatmosphären
beim Glühen verbunden
ist 1. Einen weiteren
Nachteil
stellt der möglicherweise
auftretende
Verzug
infolge
der martensitischen
Phasenumwandlung
dar, der durch eine
Nachbearbeitung
des harten Bauteils
oder einen Richtprozess
kompensiert
werden muss. Daher sind neue Konzepte
in der Entwicklung
gefordert,
die sich der Suche nach einem
sowohl
in der Herstellung
als auch in der Weiterverarbeitung
prozessschrittärmeren
Werkstoffs
entsprechender
Festigkeit
annehmen.
PROBLEMSTELLUNG UND ZIELSETZUNG
Eines dieser Konzepte
stellt die Entwicklung
eines neuartigen,
kupferlegierten
AFP-Stahls dar 2 – 4. Die wesentliche
Innovation
besteht
in der Führung
des Herstellungsprozesses
der
Halbzeuge,
die für die Massivumformung
eingesetzt
werden.
Das Halbzeug
soll aus der Walzhitze
so abgekühlt
werden, dass
die im Ferrit ausscheidungsfähigen
Anteile
an Legierungselementen
(Cu) in Lösung bleiben.
Sie werden
sich daher im Halbzeug
nur als Mischkristallverfestiger
auswirken.
Der wesentliche
ausscheidungshärtende
Beitrag
soll erst nach der Kaltumformung,
während
der Auslagerung
im Temperaturbereich
unterhalb
der Rekristallisation
des Ferrits zur Geltung
kommen.
Es werden dabei Feinstausscheidungen
in einem kalt umgeformten,
insgesamt
sehr feinkörnigen
Gefüge
erzeugt.
Es wird
Dipl.-Ing.
Frank Hoffmann
leitet die Arbeitsgruppe Stahl und
Schwermetalle am Institut
für Metallformung der TU
Bergakademie Freiberg
Prof. Dr.-Ing. Prof. E. h. mult.
Rudolf Kawalla
ist Direktor des Instituts
für Metallformung der TU
Bergakademie Freiberg
Prof. Dr.-Ing.
Ulrich Prahl
leitet die Professur für
Umformtechnik am Institut
für Metallformung der TU
Bergakademie Freiberg
angestrebt,
durch die Optimierung
der Prozessführung
die
beste Kombination
aus Festigkeit
und Zähigkeit
einzustellen.
Im Ferrit sollen dabei nur Erholungsvorgänge
stattfinden.
Die
Festigkeit
der Bauteile
(zum Beispiel
Verbindungselemente)
soll sich damit aus der Festigkeit
des Halbzeugs,
dem Betrag
der Kaltverfestigung
bei der Fertigung
durch Kaltmassivumformen
– verringert
um den Betrag
der Entfestigung
durch Erholung
im Ferrit – und der Ausscheidungshärtung
der Legierungselemente
zusammensetzen.
VORGEHENSWEISE
Die numerische
Entwicklung
eines industriell
erzeugbaren
AFP-Stahls mit niedrigem
C-Gehalt und mit Cu im Legierungsbereich
bis zirka 1,5 Prozent
wurde am Institut
für Eisenhüttenkunde
(IEHK) der RWTH Aachen durchgeführt.
Dies beinhaltete
eine thermodynamische
Simulation
zur Entwicklung
des
Mikrolegierungskonzepts
mittels ThermoCalc zur Berechnung
von Gleichgewichtsdiagrammen
sowie einer MatCalc-Simulation
zur Berechnung
der Ausscheidungskinetik.
Auf der Grundlage
dieser Simulationsergebnisse
wurden Legierungen
und
Prozessrouten
vorgeschlagen.
Anschließend
wurden Laborschmelzen
von je 80 kg hergestellt
und mithilfe
der Universalumformpresse
am Institut
für Metallformung
(imf) der TU Bergakademie
Freiberg weiterverarbeitet.
Für die Entwicklung
einer definierten
Warmumformstrategie
und
einer an die Kaltumformung
abgestimmten
Wärmebehandlungstechnologie
wurden Laboruntersuchungen
an Multifunktions
und Simulationsanlagen
Gleeble und Bähr durchgeführt.
Hierbei
bestand
das Ziel in der Ermittlung
von optimalen
Aufheizbedingungen,
der optimalen
Warmumformtemperatur
und der Bestimmung
von optimalen
Abkühlbedingungen.
Die Charakterisierung
des Lösungszustands
nach der Warmumformung
erfolgte
massivUMFORMUNG | SEPTEMBER 2018 67