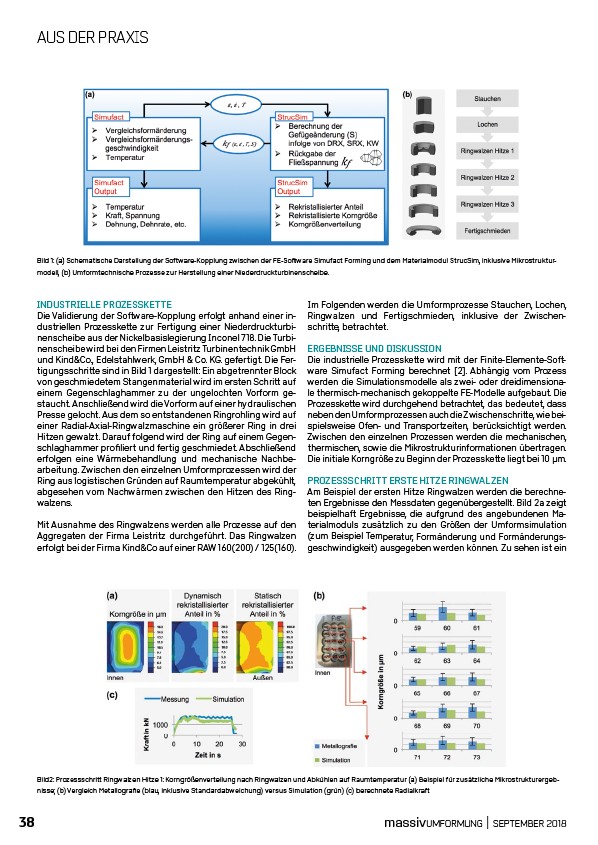
AUS DER PRAXIS
Bild 1: (a) Schematische
Darstellung
der Software
Kopplung
zwischen
der FE-Software
Simufact
Forming
und dem Materialmodul
StrucSim, inklusive
Mikrostrukturmodell,
(b) Umformtechnische
Prozesse
zur Herstellung
einer Niederdruckturbinenscheibe.
INDUSTRIELLE
PROZESSKETTE
Die Validierung
der Software
Kopplung
erfolgt
anhand
einer industriellen
Prozesskette
zur Fertigung
einer Niederdruckturbinenscheibe
aus der Nickelbasislegierung
Inconel 718. Die Turbinenscheibe
wird bei den Firmen
Leistritz Turbinentechnik
GmbH
und Kind&Co., Edelstahlwerk,
GmbH & Co. KG. gefertigt.
Die Fertigungsschritte
sind in Bild 1 dargestellt:
Ein abgetrennter
Block
von geschmiedetem
Stangenmaterial
wird im ersten
Schritt auf
einem
Gegenschlaghammer
zu der ungelochten
Vorform
gestaucht.
Anschließend
wird die Vorform
auf einer hydraulischen
Presse
gelocht.
Aus dem so entstandenen
Ringrohling
wird auf
einer Radial
Axial
Ringwalzmaschine
ein größerer
Ring in drei
Hitzen
gewalzt.
Darauf
folgend
wird der Ring auf einem
Gegenschlaghammer
profiliert
und fertig
geschmiedet.
Abschließend
erfolgen
eine Wärmebehandlung
und mechanische
Nachbearbeitung.
Zwischen
den einzelnen
Umformprozessen
wird der
Ring aus logistischen
Gründen
auf Raumtemperatur
abgekühlt,
abgesehen
vom Nachwärmen
zwischen
den Hitzen
des Ringwalzens.
Mit Ausnahme
des Ringwalzens
werden
alle
Prozesse
auf den
Aggregaten
der Firma
Leistritz durchgeführt.
Das Ringwalzen
erfolgt
bei der Firma
Kind&Co auf einer RAW 160(200) / 125(160).
Im Folgenden
werden
die Umformprozesse
Stauchen,
Lochen,
Ringwalzen
und Fertigschmieden,
inklusive
der Zwischenschritte,
betrachtet.
ERGEBNISSE
UND DISKUSSION
Die industrielle
Prozesskette
wird mit der Finite
Elemente
Software
Simufact
Forming
berechnet
2. Abhängig
vom Prozess
werden
die Simulationsmodelle
als zwei- oder dreidimensionale
thermisch
mechanisch
gekoppelte
FE-Modelle
aufgebaut.
Die
Prozesskette
wird durchgehend
betrachtet,
das bedeutet,
dass
neben
den Umformprozessen
auch die Zwischenschritte,
wie beispielsweise
Ofen- und Transportzeiten,
berücksichtigt
werden.
Zwischen
den einzelnen
Prozessen
werden
die mechanischen,
thermischen,
sowie
die Mikrostrukturinformationen
übertragen.
Die initiale
Korngröße
zu Beginn
der Prozesskette
liegt bei 10 μm.
PROZESSSCHRITT
ERSTE
HITZE
RINGWALZEN
Am Beispiel
der ersten
Hitze
Ringwalzen
werden
die berechneten
Ergebnisse
den Messdaten
gegenübergestellt.
Bild 2a zeigt
beispielhaft
Ergebnisse,
die aufgrund
des angebundenen
Materialmoduls
zusätzlich
zu den Größen
der Umformsimulation
(zum Beispiel
Temperatur,
Formänderung
und Formänderungsgeschwindigkeit)
ausgegeben
werden
können.
Zu sehen
ist ein
Bild2: Prozessschritt
Ringwalzen
Hitze
1: Korngrößenverteilung
nach Ringwalzen
und Abkühlen
auf Raumtemperatur
(a) Beispiel
für zusätzliche
Mikrostrukturergebnisse;
(b) Vergleich
Metallografie
(blau, inklusive
Standardabweichung)
versus Simulation
(grün) (c) berechnete
Radialkraft
38 massivUMFORMUNG | SEPTEMBER 2018