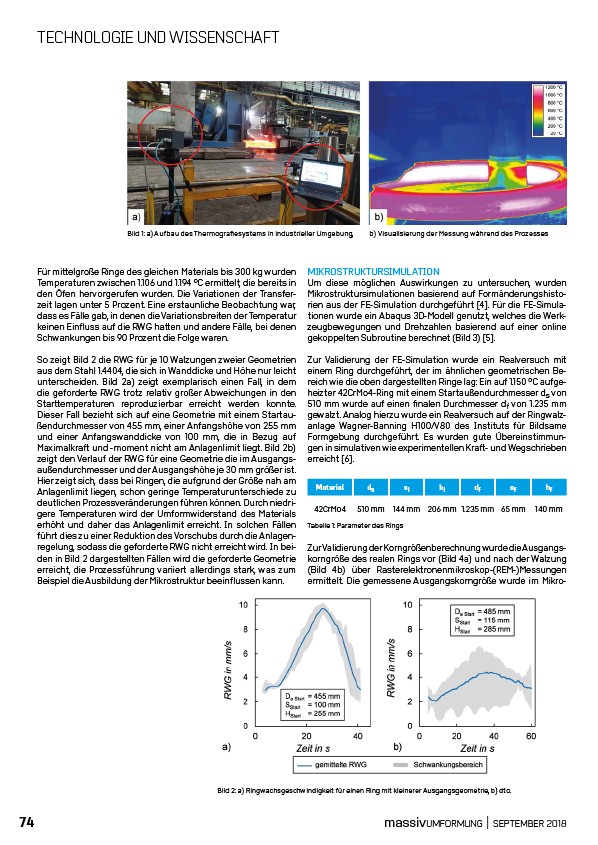
UND WISSENSCHAFT
Bild 1: a) Aufbau des Thermografiesystems in industrieller Umgebung, b) Visualisierung der Messung während des Prozesses
Für mittelgroße
Ringe des gleichen
Materials
bis 300 kg wurden
Temperaturen
zwischen
1.106 und 1.194 °C ermittelt,
die bereits
in
den Öfen hervorgerufen
wurden.
Die Variationen
der Transferzeit
lagen
unter
5 Prozent.
Eine erstaunliche
Beobachtung
war,
dass es Fälle
gab, in denen
die Variationsbreiten
der Temperatur
keinen
Einfluss
auf die RWG hatten
und andere
Fälle, bei denen
Schwankungen
bis 90 Prozent
die Folge waren.
So zeigt Bild 2 die RWG für je 10 Walzungen
zweier Geometrien
aus dem Stahl 1.4404, die sich in Wanddicke
und Höhe nur leicht
unterscheiden.
Bild 2a) zeigt exemplarisch
einen Fall, in dem
die geforderte
RWG trotz relativ
großer
Abweichungen
in den
Starttemperaturen
reproduzierbar
erreicht
werden
konnte.
Dieser
Fall bezieht
sich auf eine Geometrie
mit einem Startaußendurchmesser
von 455 mm, einer Anfangshöhe
von 255 mm
und einer Anfangswanddicke
von 100 mm, die in Bezug
auf
Maximalkraft
und -moment nicht am Anlagenlimit
liegt. Bild 2b)
zeigt den Verlauf
der RWG für eine Geometrie
die im Ausgangsaußendurchmesser
und der Ausgangshöhe
je 30 mm größer
ist.
Hier zeigt sich, dass bei Ringen,
die aufgrund
der Größe nah am
Anlagenlimit
liegen,
schon geringe
Temperaturunterschiede
zu
deutlichen
Prozessveränderungen
führen
können.
Durch niedrigere
Temperaturen
wird der Umformwiderstand
des Materials
erhöht
und daher
das Anlagenlimit
erreicht.
In solchen Fällen
führt dies zu einer Reduktion
des Vorschubs
durch die Anlagenregelung,
sodass
die geforderte
RWG nicht erreicht
wird. In beiden
in Bild 2 dargestellten
Fällen
wird die geforderte
Geometrie
erreicht,
die Prozessführung
variiert
allerdings
stark, was zum
Beispiel
die Ausbildung
der Mikrostruktur
beeinflussen
kann.
MIKROSTRUKTURSIMULATION
Um diese möglichen
Auswirkungen
zu untersuchen,
wurden
Mikrostruktursimulationen
basierend
auf Formänderungshistorien
aus der FE-Simulation
durchgeführt
4. Für die FE-Simulationen
wurde
ein Abaqus
3D-Modell
genutzt,
welches
die Werkzeugbewegungen
und Drehzahlen
basierend
auf einer online
gekoppelten
Subroutine
berechnet
(Bild 3) 5.
Zur Validierung
der FE-Simulation
wurde
ein Realversuch
mit
einem Ring durchgeführt,
der im ähnlichen
geometrischen
Bereich
wie die oben dargestellten
Ringe lag: Ein auf 1.150 °C aufgeheizter
42CrMo4-Ring mit einem Startaußendurchmesser
ds von
510 mm wurde
auf einen finalen
Durchmesser
df von 1.235 mm
gewalzt. Analog hierzu
wurde
ein Realversuch
auf der Ringwalzanlage
Wagner
Banning H100/V80 des Instituts
für Bildsame
Formgebung
durchgeführt.
Es wurden
gute Übereinstimmungen
in simulativen
wie experimentellen Kraft- und Wegschrieben
erreicht 6.
Material ds si hi df sf hf
42CrMo4 510 mm 144 mm 206 mm 1.235 mm 65 mm 140 mm
Tabelle 1: Parameter des Rings
Zur Validierung der Korngrößenberechnung
wurde die Ausgangskorngröße
des realen Rings vor (Bild 4a) und nach der Walzung
(Bild 4b) über Rasterelektronenmikroskop(
REM-)Messungen
ermittelt.
Die gemessene
Ausgangskorngröße
wurde im MikroTECHNOLOGIE
Bild 2: a) Ringwachsgeschwindigkeit für einen Ring mit kleinerer Ausgangsgeometrie, b) dto.
74 massivUMFORMUNG | SEPTEMBER 2018