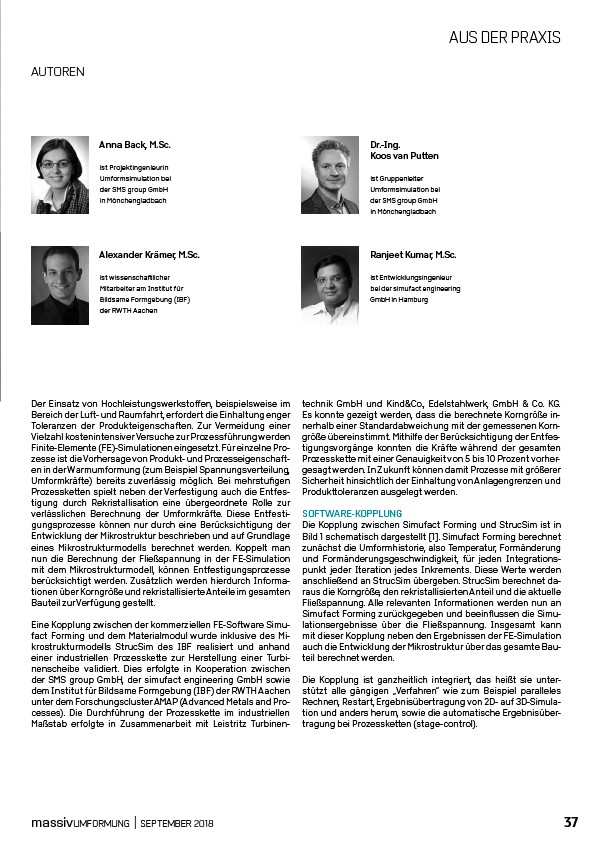
AUTOREN
Anna Back, M.Sc.
ist Projektingenieurin
Umformsimulation bei
der SMS group GmbH
in Mönchengladbach
Alexander Krämer, M.Sc.
ist wissenschaftlicher
Mitarbeiter am Institut für
Bildsame Formgebung (IBF)
der RWTH Aachen
Der Einsatz
von Hochleistungswerkstoffen,
beispielsweise
im
Bereich
der Luft- und Raumfahrt,
erfordert
die Einhaltung
enger
Toleranzen
der Produkteigenschaften.
Zur Vermeidung
einer
Vielzahl
kostenintensiver
Versuche
zur Prozessführung
werden
Finite
Elemente
(FE)-Simulationen
eingesetzt.
Für einzelne
Prozesse
ist die Vorhersage
von Produkt
und Prozesseigenschaften
in der Warmumformung
(zum Beispiel
Spannungsverteilung,
Umformkräfte)
bereits
zuverlässig
möglich.
Bei mehrstufigen
Prozessketten
spielt neben
der Verfestigung
auch die Entfestigung
durch Rekristallisation
eine übergeordnete
Rolle zur
verlässlichen
Berechnung
der Umformkräfte.
Diese
Entfestigungsprozesse
können
nur durch eine Berücksichtigung
der
Entwicklung
der Mikrostruktur
beschrieben
und auf Grundlage
eines Mikrostrukturmodells
berechnet
werden. Koppelt
man
nun die Berechnung
der Fließspannung
in der FE-Simulation
mit dem Mikrostrukturmodell, können Entfestigungsprozesse
berücksichtigt
werden. Zusätzlich
werden
hierdurch
Informationen
über Korngröße
und rekristallisierte
Anteile
im gesamten
Bauteil
zur Verfügung
gestellt.
Eine Kopplung
zwischen
der kommerziellen
FE-Software
Simufact
Forming
und dem Materialmodul
wurde inklusive
des Mikrostrukturmodells
StrucSim
des IBF realisiert
und anhand
einer industriellen
Prozesskette
zur Herstellung
einer Turbinenscheibe
validiert.
Dies erfolgte
in Kooperation
zwischen
der SMS group GmbH, der simufact
engineering
GmbH sowie
dem Institut
für Bildsame
Formgebung
(IBF) der RWTH Aachen
unter dem Forschungscluster
AMAP (Advanced
Metals and Processes).
Die Durchführung
der Prozesskette
im industriellen
Maßstab
erfolgte
in Zusammenarbeit
mit Leistritz Turbinentechnik
AUS DER PRAXIS
Dr.-Ing.
Koos van Putten
ist Gruppenleiter
Umformsimulation bei
der SMS group GmbH
in Mönchengladbach
Ranjeet Kumar, M.Sc.
ist Entwicklungsingenieur
bei der simufact engineering
GmbH in Hamburg
GmbH und Kind&Co., Edelstahlwerk,
GmbH & Co. KG.
Es konnte
gezeigt
werden, dass die berechnete
Korngröße
innerhalb
einer Standardabweichung
mit der gemessenen
Korngröße
übereinstimmt.
Mithilfe
der Berücksichtigung
der Entfestigungsvorgänge
konnten die Kräfte während
der gesamten
Prozesskette
mit einer Genauigkeit
von 5 bis 10 Prozent
vorhergesagt
werden. In Zukunft
können
damit Prozesse
mit größerer
Sicherheit
hinsichtlich
der Einhaltung
von Anlagengrenzen
und
Produkttoleranzen
ausgelegt
werden.
SOFTWARE
KOPPLUNG
Die Kopplung
zwischen Simufact
Forming
und StrucSim
ist in
Bild 1 schematisch
dargestellt
1. Simufact
Forming
berechnet
zunächst
die Umformhistorie,
also Temperatur,
Formänderung
und Formänderungsgeschwindigkeit,
für jeden
Integrationspunkt
jeder
Iteration
jedes
Inkrements.
Diese Werte
werden
anschließend
an StrucSim
übergeben.
StrucSim
berechnet
daraus
die Korngröße,
den rekristallisierten
Anteil
und die aktuelle
Fließspannung.
Alle relevanten
Informationen
werden
nun an
Simufact
Forming
zurückgegeben
und beeinflussen
die Simulationsergebnisse
über die Fließspannung.
Insgesamt
kann
mit dieser Kopplung
neben
den Ergebnissen
der FE-Simulation
auch die Entwicklung
der Mikrostruktur
über das gesamte
Bauteil
berechnet
werden.
Die Kopplung
ist ganzheitlich
integriert,
das heißt sie unterstützt
alle gängigen
„Verfahren“
wie zum Beispiel
paralleles
Rechnen,
Restart,
Ergebnisübertragung
von 2D- auf 3D-Simulation
und anders
herum,
sowie die automatische
Ergebnisübertragung
bei Prozessketten
(stage-control).
massivUMFORMUNG | SEPTEMBER 2018 37