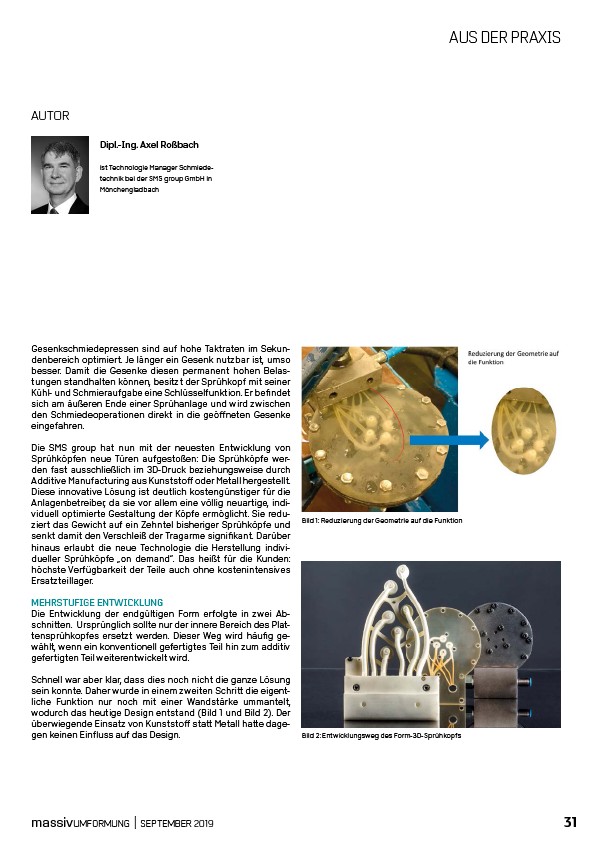
AUTOR
Dipl.-Ing. Axel Roßbach
ist Technologie
Manager
Schmiedetechnik
bei der SMS group GmbH in
Mönchengladbach
AUS DER PRAXIS
Gesenkschmiedepressen
sind auf hohe
Taktraten
im Sekundenbereich
optimiert.
Je länger
ein Gesenk
nutzbar
ist, umso
besser.
Damit
die Gesenke
diesen
permanent
hohen
Belastungen
standhalten
können,
besitzt
der Sprühkopf
mit seiner
Kühl- und Schmieraufgabe
eine
Schlüsselfunktion.
Er befindet
sich am äußeren
Ende
einer
Sprühanlage
und wird zwischen
den Schmiedeoperationen
direkt
in die geöffneten
Gesenke
eingefahren.
Die SMS group hat nun mit der neuesten
Entwicklung
von
Sprühköpfen
neue Türen
aufgestoßen:
Die Sprühköpfe
werden
fast ausschließlich
im 3D-Druck beziehungsweise
durch
Additive
Manufacturing
aus Kunststoff
oder Metall
hergestellt.
Diese
innovative
Lösung
ist deutlich
kostengünstiger
für die
Anlagenbetreiber,
da sie vor allem
eine
völlig
neuartige,
individuell
optimierte
Gestaltung
der Köpfe
ermöglicht.
Sie reduziert
das Gewicht
auf ein Zehntel
bisheriger
Sprühköpfe
und
senkt damit
den Verschleiß
der Tragarme
signifikant.
Darüber
hinaus
erlaubt
die neue Technologie
die Herstellung
individueller
Sprühköpfe
„on demand“.
Das heißt für die Kunden:
höchste
Verfügbarkeit
der Teile
auch ohne
kostenintensives
Ersatzteillager.
MEHRSTUFIGE ENTWICKLUNG
Die Entwicklung
der endgültigen
Form erfolgte
in zwei Abschnitten.
Ursprünglich
sollte
nur der innere
Bereich
des Plattensprühkopfes
ersetzt
werden.
Dieser
Weg wird häufig
gewählt,
wenn ein konventionell
gefertigtes
Teil hin zum additiv
gefertigten
Teil weiterentwickelt
wird.
Schnell war aber klar, dass dies noch nicht die ganze
Lösung
sein konnte.
Daher
wurde
in einem
zweiten
Schritt die eigentliche
Funktion
nur noch mit einer
Wandstärke
ummantelt,
wodurch
das heutige
Design
entstand
(Bild 1 und Bild 2). Der
überwiegende
Einsatz
von Kunststoff
statt Metall
hatte
dagegen
keinen
Einfluss
auf das Design.
Bild 1: Reduzierung
der Geometrie
auf die Funktion
Bild 2: Entwicklungsweg
des Form-3D-Sprühkopfs
massivUMFORMUNG | SEPTEMBER 2019 31