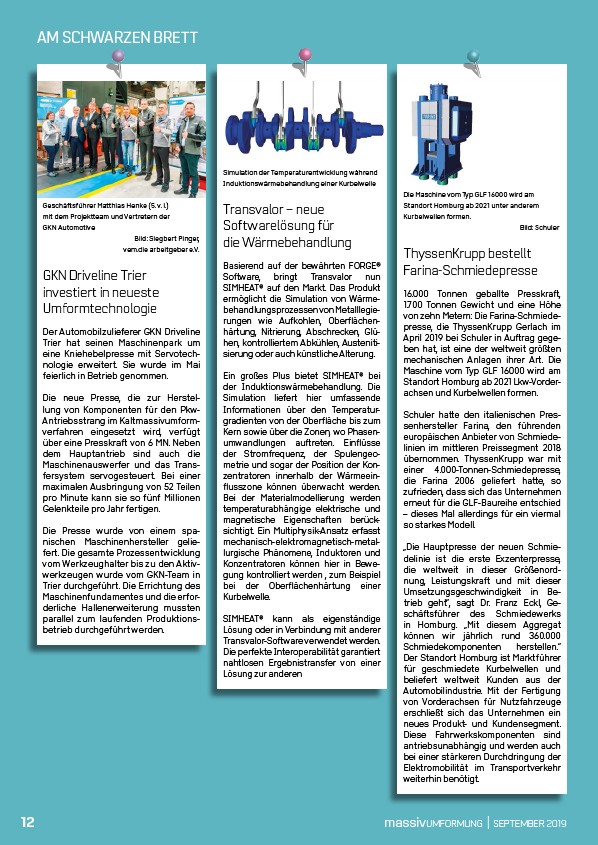
AM SCHWARZEN BRETT
Geschäftsführer Matthias Henke (5. v. l.)
mit dem Projektteam und Vertretern der
GKN Automotive
Bild: Siegbert Pinger,
vem.die arbeitgeber e. V.
GKN Driveline Trier
investiert in neueste
Umformtechnologie
Der Automobilzulieferer
GKN Driveline
Trier hat seinen Maschinenpark
um
eine Kniehebelpresse
mit Servotechnologie
erweitert.
Sie wurde im Mai
feierlich in Betrieb genommen.
Die neue Presse, die zur Herstellung
von Komponenten
für den Pkw-
Antriebsstrang
im Kaltmassivumformverfahren
eingesetzt
wird, verfügt
über eine Presskraft
von 6 MN. Neben
dem Hauptantrieb
sind auch die
Maschinenauswerfer
und das Transfersystem
servogesteuert.
Bei einer
maximalen
Ausbringung
von 52 Teilen
pro Minute kann sie so fünf Millionen
Gelenkteile
pro Jahr fertigen.
Die Presse wurde von einem spanischen
Maschinenhersteller
geliefert.
Die gesamte Prozessentwicklung
vom Werkzeughalter
bis zu den Aktivwerkzeugen
wurde vom GKN-Team in
Trier durchgeführt.
Die Errichtung
des
Maschinenfundamentes
und die erforderliche
Hallenerweiterung
mussten
parallel zum laufenden
Produktionsbetrieb
durchgeführt
werden.
Die Maschine vom Typ GLF 16000 wird am
Standort Homburg ab 2021 unter anderem
Kurbelwellen formen.
Bild: Schuler
ThyssenKrupp bestellt
Farina-Schmiedepresse
16.000 Tonnen geballte Presskraft,
1.700 Tonnen Gewicht und eine Höhe
von zehn Metern: Die Farina-Schmiedepresse,
die ThyssenKrupp Gerlach im
April 2019 bei Schuler in Auft
rag gegeben
hat, ist eine der weltweit
größten
mechanischen
Anlagen
ihrer Art. Die
Maschine vom Typ GLF 16000 wird am
Standort
Homburg
ab 2021 Lkw-Vorderachsen
und Kurbelwellen
formen.
Schuler hatte den italienischen Pressenhersteller
Farina, den führenden
europäischen
Anbieter von Schmiedelinien
im mittleren Preissegment
2018
übernommen.
ThyssenKrupp war mit
einer 4.000-Tonnen-Schmiedepresse,
die Farina 2006 geliefert
hatte, so
zufrieden,
dass sich das Unternehmen
erneut für die GLF-Baureihe
entschied
– dieses Mal allerdings
für ein viermal
so starkes Modell.
„Die Hauptpresse
der neuen Schmiedelinie
ist die erste Exzenterpresse,
die weltweit
in dieser Größenordnung,
Leistungskraft
und mit dieser
Umsetzungsgeschwindigkeit
in Betrieb
geht“, sagt Dr. Franz Eckl, Geschäftsführer
des Schmiedewerks
in Homburg. „Mit diesem Aggregat
können wir jährlich rund 360.000
Schmiedekomponenten
herstellen.“
Der Standort Homburg ist Marktführer
für geschmiedete
Kurbelwellen
und
beliefert weltweit
Kunden aus der
Automobilindustrie.
Mit der Fertigung
von Vorderachsen
für Nutzfahrzeuge
erschließt sich das Unternehmen
ein
neues Produkt
und Kundensegment.
Diese Fahrwerkskomponenten
sind
antriebsunabhängig
und werden auch
bei einer stärkeren Durchdringung
der
Elektromobilität
im Transportverkehr
weiterhin
benötigt.
Simulation der Temperaturentwicklung während
Induktionswärmebehandlung einer Kurbelwelle
Transvalor – neue
Softwarelösung für
die Wärmebehandlung
Basierend auf der bewährten
FORGE®
Software,
bringt Transvalor nun
SIMHEAT® auf den Markt. Das Produkt
ermöglicht
die Simulation
von Wärmebehandlungsprozessen
von Metalllegierungen
wie Aufkohlen,
Oberflächenhärtung,
Nitrierung,
Abschrecken, Glühen,
kontrolliertem
Abkühlen, Austenitisierung
oder auch künstliche
Alterung.
Ein großes Plus bietet SIMHEAT® bei
der Induktionswärmebehandlung.
Die
Simulation
liefert hier umfassende
Informationen
über den Temperaturgradienten
von der Oberfläche
bis zum
Kern sowie über die Zonen, wo Phasenumwandlungen
auft
reten. Einflüsse
der Stromfrequenz,
der Spulengeometrie
und sogar der Position
der Konzentratoren
innerhalb
der Wärmeeinflusszone
können überwacht
werden.
Bei der Materialmodellierung
werden
temperaturabhängige
elektrische
und
magnetische
Eigenschaften
berücksichtigt.
Ein Multiphysik-Ansatz erfasst
mechanisch
elektromagnetisch
metallurgische
Phänomene,
Induktoren
und
Konzentratoren
können hier in Bewegung
kontrolliert
werden , zum Beispiel
bei der Oberflächenhärtung
einer
Kurbelwelle.
SIMHEAT® kann als eigenständige
Lösung oder in Verbindung
mit anderer
Transvalor-Software
verwendet
werden.
Die perfekte Interoperabilität
garantiert
nahtlosen
Ergebnistransfer
von einer
Lösung zur anderen
12 massivUMFORMUNG | SEPTEMBER 2019