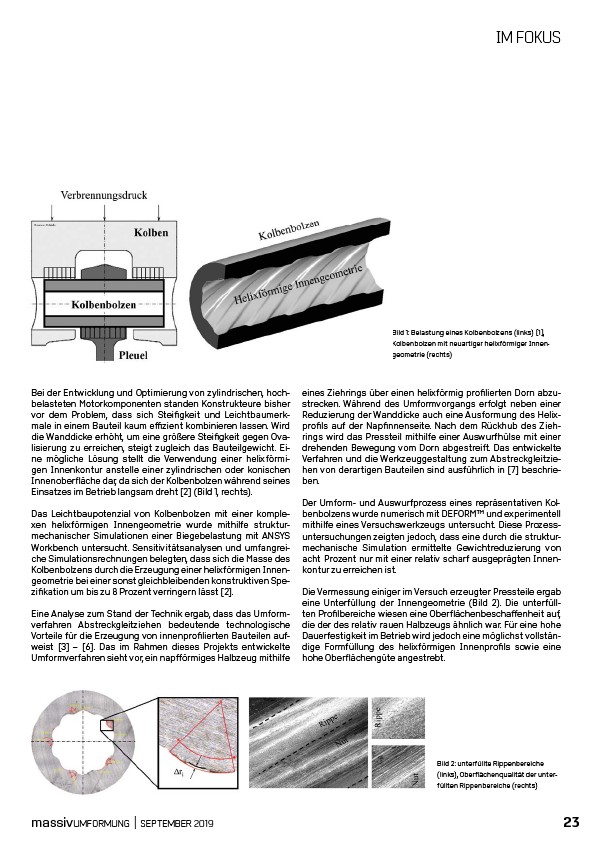
IM FOKUS
Bild 1: Belastung
eines
Kolbenbolzens
(links) 1,
Kolbenbolzen
mit neuartiger
helixförmiger
Innengeometrie
(rechts)
Bei der Entwicklung
und Optimierung
von zylindrischen,
hochbelasteten
Motorkomponenten
standen
Konstrukteure
bisher
vor dem Problem,
dass sich Steifigkeit
und Leichtbaumerkmale
in einem
Bauteil
kaum effizient
kombinieren
lassen.
Wird
die Wanddicke
erhöht,
um eine
größere
Steifigkeit
gegen
Ovalisierung
zu erreichen,
steigt zugleich
das Bauteilgewicht.
Eine
mögliche
Lösung
stellt die Verwendung
einer
helixförmigen
Innenkontur
anstelle
einer
zylindrischen
oder konischen
Innenoberfläche
dar, da sich der Kolbenbolzen
während
seines
Einsatzes
im Betrieb
langsam
dreht 2 (Bild 1, rechts).
Das Leichtbaupotenzial
von Kolbenbolzen
mit einer
komplexen
helixförmigen
Innengeometrie
wurde
mithilfe
strukturmechanischer
Simulationen
einer
Biegebelastung
mit ANSYS
Workbench untersucht.
Sensitivitätsanalysen
und umfangreiche
Simulationsrechnungen
belegten,
dass sich die Masse
des
Kolbenbolzens
durch die Erzeugung
einer
helixförmigen
Innengeometrie
bei einer
sonst gleichbleibenden
konstruktiven
Spezifikation
um bis zu 8 Prozent
verringern
lässt 2.
Eine
Analyse
zum Stand der Technik
ergab,
dass das Umformverfahren
Abstreckgleitziehen
bedeutende
technologische
Vorteile
für die Erzeugung
von innenprofilierten
Bauteilen
aufweist
3 – 6. Das im Rahmen
dieses
Projekts
entwickelte
Umformverfahren
sieht vor, ein napfförmiges
Halbzeug
mithilfe
eines
Ziehrings
über einen
helixförmig
profilierten
Dorn abzustrecken.
Während
des Umformvorgangs
erfolgt
neben
einer
Reduzierung
der Wanddicke
auch eine
Ausformung
des Helixprofils
auf der Napfinnenseite.
Nach dem Rückhub
des Ziehrings
wird das Pressteil
mithilfe
einer
Auswurfhülse
mit einer
drehenden
Bewegung
vom Dorn abgestreift.
Das entwickelte
Verfahren
und die Werkzeuggestaltung
zum Abstreckgleitziehen
von derartigen
Bauteilen
sind ausführlich
in 7 beschrieben.
Der Umform
und Auswurfprozess
eines
repräsentativen
Kolbenbolzens
wurde
numerisch
mit DEFORMTM und experimentell
mithilfe
eines
Versuchswerkzeugs
untersucht.
Diese
Prozessuntersuchungen
zeigten
jedoch,
dass eine
durch die strukturmechanische
Simulation
ermittelte
Gewichtreduzierung
von
acht Prozent
nur mit einer
relativ
scharf ausgeprägten
Innenkontur
zu erreichen
ist.
Die Vermessung
einiger
im Versuch
erzeugter
Pressteile
ergab
eine
Unterfüllung
der Innengeometrie
(Bild 2). Die unterfüllten
Profilbereiche
wiesen
eine
Oberflächenbeschaffenheit
auf,
die der des relativ
rauen
Halbzeugs
ähnlich
war. Für eine
hohe
Dauerfestigkeit
im Betrieb
wird jedoch
eine
möglichst
vollständige
Formfüllung
des helixförmigen
Innenprofils
sowie
eine
hohe Oberflächengüte
angestrebt.
Bild 2: unterfüllte
Rippenbereiche
(links), Oberflächenqualität
der unterfüllten
Rippenbereiche
(rechts)
massivUMFORMUNG | SEPTEMBER 2019 23